Understanding Parker hydraulic pumps is of utmost importance for industries relying on these critical components. In this guide, we will provide a comprehensive overview of the construction, operation, and maintenance of Parker hydraulic pumps. By demystifying these intricate devices, we aim to equip readers with the knowledge necessary to ensure optimal performance and longevity. Hydraulic pumps are essential in various applications, powering machinery and enabling efficient operations. With this guide, we seek to shed light on the inner workings of Parker hydraulic pumps, empowering industries to make informed decisions and maximize the potential of these vital components.
Understanding Hydraulic Pumps
To grasp the significance of Parker hydraulic pumps, it is essential to understand the fundamentals of hydraulic systems and the pivotal role that hydraulic pumps play within them. Hydraulic systems utilize the power of fluid to transmit force and control motion, making them integral to a wide range of applications.
Hydraulic pumps serve as the heart of these systems, converting mechanical power into hydraulic energy. They generate the necessary pressure to drive the fluid through the system, enabling it to perform work. Acting as the primary power source, hydraulic pumps supply pressurized fluid to cylinders, motors, or other hydraulic devices.
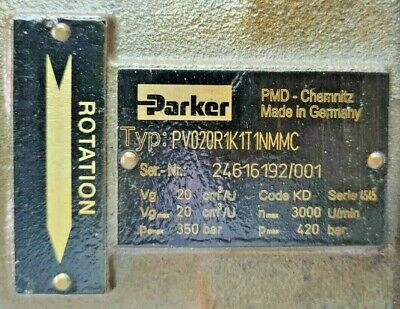
Understanding the construction, operation, and maintenance of hydraulic pumps is vital. Hydraulic pumps create flow and generate the required pressure to power the system. When the pump is activated, it draws in fluid from a reservoir and forces it into the hydraulic circuit. This action creates a continuous flow of fluid, empowering various components and actuators within the system to perform their intended functions.
Choosing the right hydraulic pump is of utmost importance for optimal system performance. Different applications require specific pump characteristics, such as flow rate, pressure capabilities, and efficiency. The selection of the appropriate pump directly impacts the reliability, efficiency, and overall productivity of the system.
By delving into the construction, operation, and maintenance of hydraulic pumps, readers will gain a comprehensive understanding of these crucial components. This knowledge will enable them to make informed decisions when selecting Parker hydraulic pumps and ensure their efficient and effective utilization in diverse industries and applications.

Construction of Parker Hydraulic Pumps
Understanding the construction of Parker hydraulic pumps provides valuable insights into their design elements, components, and manufacturing processes. Here are key aspects to consider:
- Components and Design Elements: Parker hydraulic pumps consist of various essential components, including a housing, internal gears, vanes, pistons, swashplates, valves, and seals. These components work together to create the pumping action and fluid displacement necessary for hydraulic systems.
- Quality Materials: Parker prioritizes the use of high-quality materials in the construction of their hydraulic pumps. This ensures durability, longevity, and resistance to wear and corrosion. Robust materials contribute to the reliable performance of the pump even in demanding operating conditions.
- Manufacturing Processes: Parker employs advanced manufacturing processes to produce hydraulic pumps of exceptional quality. Precision machining, stringent quality control, and adherence to industry standards ensure that each pump meets the highest performance and reliability standards.
- Design Features: Parker hydraulic pumps incorporate design features that enhance their efficiency and performance. These features may include optimized fluid flow paths, advanced sealing mechanisms, and innovative designs for reduced noise and vibration.
Understanding the construction of Parker hydraulic pumps helps users appreciate the craftsmanship and engineering behind these essential components. Quality materials, precision manufacturing, and thoughtful design elements contribute to the reliable and efficient performance of Parker hydraulic pumps in a wide range of applications.
Operation of Parker Hydraulic Pumps
To understand the operation of Parker hydraulic pumps, it is important to grasp their functioning principles, fluid displacement process, and pressure generation and control. Here’s a breakdown of their operation:
- Functioning Principles: Parker hydraulic pumps operate based on the principles of fluid mechanics. They utilize mechanical power, typically from an electric motor or an engine, to drive the pump’s internal components and generate fluid flow and pressure.
- Fluid Displacement Process: When the hydraulic pump is activated, it creates a mechanical action that moves the hydraulic fluid. This displacement creates a continuous flow of pressurized fluid, which is crucial for powering various hydraulic components and performing work within the system.
- Pressure Generation and Control: Parker hydraulic pumps are designed to generate the necessary pressure required for specific applications. As the fluid is displaced, pressure is built within the system, enabling the hydraulic system to perform tasks such as lifting, pushing, or rotating machinery.
To control the pressure, hydraulic pumps may incorporate pressure relief valves or pressure-compensated controls. These mechanisms ensure that the system operates within the desired pressure range and provide safety measures to prevent overloading or damage to the system.
Parker hydraulic pumps rely on precision engineering and design to ensure efficient and reliable operation. By understanding their functioning principles, fluid displacement process, and pressure generation and control, users can make informed decisions when selecting and utilizing Parker hydraulic pumps in various applications.
Types of Parker Hydraulic Pumps
Parker offers a wide range of hydraulic pumps, each designed to meet specific application requirements. Understanding the different types of Parker hydraulic pumps is crucial for selecting the most suitable option. Here are some key types:
- Gear Pumps: Gear pumps are known for their simplicity and reliability. They consist of two intermeshing gears that create a pumping action, delivering a steady flow of fluid. Gear pumps are suitable for low-to-medium pressure applications and find common usage in industries such as agriculture, construction, and material handling.
- Vane Pumps: Vane pumps utilize sliding vanes that create chambers to pump fluid. They offer high efficiency, smooth operation, and low noise levels. Vane pumps are versatile and find applications in machine tools, injection molding, and automotive systems.
- Piston Pumps: Piston pumps provide high-pressure capabilities and are commonly used in heavy-duty applications. They feature reciprocating pistons driven by a swashplate or a cam mechanism, generating fluid displacement. Piston pumps excel in industries such as mining, oil and gas, and aerospace, where robust performance is essential.
- Axial Piston Pumps: Axial piston pumps feature a barrel-shaped housing with pistons arranged in an axial manner. They offer excellent efficiency, high pressure capabilities, and precise control. Axial piston pumps are commonly used in hydraulic power units, industrial machinery, and mobile equipment.
- Radial Piston Pumps: Radial piston pumps have pistons arranged radially around a central eccentric shaft. They provide high-pressure capabilities, compact design, and smooth operation. Radial piston pumps find applications in machine tools, presses, and hydraulic test rigs.
Each type of Parker hydraulic pump has its own unique design, functionality, and benefits. The selection of the appropriate pump depends on factors such as flow rate, pressure requirements, efficiency, and specific application needs. Parker’s diverse range of hydraulic pumps ensures that there is an ideal solution for various industries and applications, delivering reliable and efficient hydraulic power.
Maintenance of Parker Hydraulic Pumps
Proper maintenance is essential for ensuring the optimal performance and longevity of Parker hydraulic pumps. Here are some recommended maintenance practices:
- Regular Maintenance Schedule: Establish a regular maintenance schedule for the hydraulic pump. Follow the manufacturer’s guidelines for routine maintenance tasks, including inspection, lubrication, and replacement of worn-out components.
- Visual Inspection: Conduct visual inspections of the pump regularly. Check for any signs of leaks, loose connections, or damage to the pump or its components. Pay attention to seals, hoses, and fittings for any wear or deterioration.
- Lubrication: Proper lubrication is crucial for the smooth operation of hydraulic pumps. Follow the manufacturer’s recommendations for lubricating the pump’s moving parts. Use the recommended lubricants and ensure they are applied in the correct quantity and intervals.
- Fluid Analysis: Monitor the quality of the hydraulic fluid regularly. Perform fluid analysis to check for contamination, moisture content, and viscosity. Contaminated or degraded fluid can affect pump performance and lead to system damage.
- Filter Replacement: Regularly replace or clean the hydraulic filters as per the manufacturer’s recommendations. Clogged or dirty filters restrict the flow of fluid and can cause pump inefficiencies or damage.
- Proper Storage: If the pump is not in use, store it in a clean and dry environment. Protect it from dust, moisture, and extreme temperatures. Follow the manufacturer’s guidelines for proper storage procedures.
- Troubleshooting: Familiarize yourself with common issues that may arise with hydraulic pumps. If you encounter any problems, promptly troubleshoot and identify the root cause. Refer to the manufacturer’s troubleshooting guide or seek professional assistance when needed.
- Professional Servicing: For complex maintenance tasks or major repairs, it is advisable to seek professional servicing. Experienced technicians can provide expert advice, diagnose issues accurately, and ensure proper repairs and maintenance.
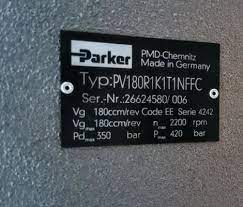
By following these maintenance practices, you can maximize the performance, reliability, and lifespan of Parker hydraulic pumps. Regular maintenance helps identify and address potential issues before they escalate, reducing downtime and costly repairs.
Troubleshooting and Common Issues
Despite regular maintenance, hydraulic pumps may encounter issues that require troubleshooting. Here are some common problems that may arise with Parker hydraulic pumps and techniques for resolving them:
- Low Flow or No Flow: Insufficient or no fluid flow can indicate a clogged filter, damaged pump components, or an airlock in the system. Check the filter for blockages and clean or replace it if necessary. Inspect the pump for any damaged or worn-out parts. Bleed the air from the system to restore proper flow.
- Excessive Noise or Vibration: Unusual noise or vibration can be caused by loose fittings, worn-out bearings, cavitation, or misalignment. Inspect the fittings and tighten them as needed. Check the bearings for wear and replace them if necessary. Ensure proper alignment of the pump and its components.
- Fluid Leakage: Fluid leakage can occur due to damaged seals, worn-out O-rings, or loose connections. Inspect the seals and O-rings for any signs of damage and replace them if needed. Tighten loose connections and ensure proper sealing.
- Overheating: Overheating can be caused by excessive system pressure, low fluid levels, or inadequate cooling. Check the pressure settings and adjust them if necessary. Monitor the fluid levels and ensure they are within the recommended range. Verify that the cooling system is functioning properly and address any issues with the cooling mechanism.
- Erratic Operation: Erratic operation, such as inconsistent flow or pressure, can be due to issues with the pump’s control mechanism, worn-out components, or contamination in the system. Inspect the control mechanism and adjust or replace it as needed. Check for any worn-out or damaged components and address them accordingly. Flush and clean the system to remove contaminants.
- System Failure: Complete system failure may occur due to severe damage to the pump or other components. In such cases, it is recommended to seek professional assistance from qualified technicians. They can diagnose the root cause of the failure and perform necessary repairs or replacements.
It is important to remember that troubleshooting hydraulic pumps requires knowledge and expertise. If you encounter issues that you are unable to resolve or if the problem persists, it is advisable to consult a professional hydraulic technician. Their expertise will ensure accurate diagnosis and effective resolution of the problem, minimizing downtime and preventing further damage.
Best Practices for Parker Hydraulic Pump Maintenance
To ensure the optimal performance and longevity of Parker hydraulic pumps, it is important to follow best practices for maintenance. Here are some guidelines to help you maintain your hydraulic pumps effectively:
- Adhere to Manufacturer’s Recommendations: Follow the maintenance guidelines provided by Parker for your specific hydraulic pump model. These recommendations are tailored to ensure proper care and maintenance of the pump.
- Regular Inspections: Conduct routine visual inspections of the pump to check for any signs of leaks, damage, or wear. Inspect the fittings, seals, hoses, and other components for any abnormalities. Early detection of issues allows for timely repairs or replacements.
- Cleanliness: Keep the pump and its surroundings clean to prevent the ingress of dirt, dust, and debris. Regularly clean the pump using appropriate cleaning agents and methods recommended by the manufacturer.
- Lubrication: Follow the lubrication schedule provided by the manufacturer. Proper lubrication of moving parts, such as bearings and gears, ensures smooth operation and minimizes wear. Use the recommended lubricants and apply them in the correct quantity and intervals.
- Filter Maintenance: Regularly inspect and clean or replace the hydraulic filters as per the manufacturer’s recommendations. Clean filters ensure proper fluid flow and prevent contaminants from entering the pump and other components.
- Temperature Control: Monitor the operating temperature of the hydraulic system and keep it within the recommended range. Excessive heat can degrade the hydraulic fluid and adversely affect pump performance. Use proper cooling mechanisms, such as fans or heat exchangers, if required.
- Proper Handling: Follow proper handling procedures when working with hydraulic pumps. Avoid excessive force, impacts, or mishandling that can cause damage. Use appropriate lifting equipment and techniques to prevent accidents and injuries.
- Training and Expertise: Ensure that personnel responsible for pump maintenance are properly trained and have the necessary expertise. Training in hydraulic systems, maintenance procedures, and safety practices is essential for effective maintenance and troubleshooting.
By following these best practices, you can optimize the performance and lifespan of your Parker hydraulic pumps. Regular maintenance, adherence to manufacturer’s recommendations, and proper handling contribute to reliable and efficient pump operation, reducing downtime and minimizing costly repairs.
Related Keywords
# parker hydraulic pump,
# parker hydraulic pumps,
# hydraulic pump parker,
# parker pumps,
# parker hydraulic motors,
# hydraulic motors parker,
# parker hydraulic pumps catalog,
vparker hydraulic pump catalog,