Understanding the engineering principles behind Caterpillar hydraulic pumps is essential for efficiently utilizing these hydraulic systems. By comprehending the design and operation aspects, users can maximize the performance and reliability of these pumps. In this outline, we will delve into the fundamentals of hydraulic systems, the design and construction of Caterpillar hydraulic pumps, their performance and efficiency, operating principles, control and regulation, and more. By gaining a comprehensive understanding of these engineering principles, users can harness the full potential of Caterpillar hydraulic pumps in various applications.
Fundamentals of Hydraulic Systems
Hydraulic systems operate on the principles of fluid power, utilizing hydraulic pumps as the primary components. These systems generate and transmit power using pressurized fluid, typically oil or hydraulic fluid. The hydraulic pump plays a crucial role in converting mechanical power into hydraulic power.
Within a hydraulic system, the pump creates flow and pressure by drawing in fluid from a reservoir and forcing it into the hydraulic circuit. This pressurized fluid is then used to perform work, such as operating cylinders, motors, or other hydraulic devices.
Understanding the fundamentals of hydraulic systems is essential for comprehending the role and significance of hydraulic pumps in Caterpillar equipment. It involves grasping concepts such as pressure, flow, and control, as they relate to the efficient operation and performance of hydraulic systems.
By studying the fundamentals, users can gain insights into how hydraulic pumps generate fluid power and how different pump types, such as gear pumps, vane pumps, and piston pumps, contribute to varying performance characteristics. This knowledge lays the foundation for effectively utilizing Caterpillar hydraulic pumps in diverse applications, ensuring optimal system operation and productivity.
Design and Construction of Caterpillar Hydraulic Pumps
Caterpillar hydraulic pumps are meticulously designed and engineered to meet the demanding requirements of various industries. The design considerations and engineering principles behind these pumps are crucial for their efficient and reliable performance.
The design process begins with a thorough analysis of the application requirements, taking into account factors such as flow rate, pressure, and operating conditions. Caterpillar engineers employ advanced modeling and simulation techniques to optimize the pump’s design and ensure it meets the desired performance parameters.
In terms of construction, Caterpillar hydraulic pumps are built with high-quality materials and components. The pump housing, rotor, vanes, pistons, valves, and other essential elements are precisely manufactured to strict tolerances. This precision ensures smooth operation, minimizing internal leakage and maximizing volumetric efficiency.
Additionally, Caterpillar focuses on incorporating innovative features into their hydraulic pumps. These features may include advanced sealing technologies to enhance durability and performance, as well as optimized internal flow paths for improved efficiency. By leveraging cutting-edge design and construction techniques, Caterpillar hydraulic pumps deliver exceptional reliability, longevity, and performance in various applications.
Understanding the design and construction principles of Caterpillar hydraulic pumps is crucial for proper pump selection, installation, and maintenance. It enables users to make informed decisions and ensures optimal pump performance and longevity in their hydraulic systems.
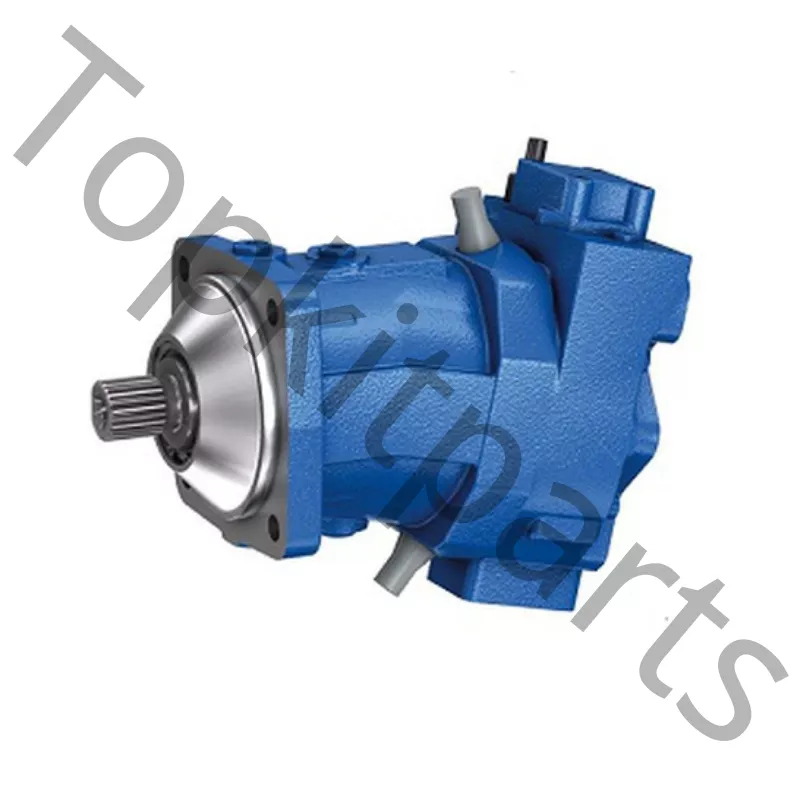
Pump Performance and Efficiency
The performance and efficiency of Caterpillar hydraulic pumps are key considerations in their design and operation. These pumps are engineered to deliver high performance while maximizing energy efficiency.
One important aspect of pump performance is volumetric efficiency, which measures the pump’s ability to deliver a consistent flow rate. Caterpillar hydraulic pumps are designed with tight clearances and precision-machined components to minimize internal leakage and maximize volumetric efficiency. This ensures that the pump can deliver the required flow rate without unnecessary energy losses.
Efficiency is another critical factor in pump operation. Caterpillar employs advanced design techniques to reduce mechanical losses and improve overall efficiency. By optimizing the internal flow paths, minimizing friction, and using efficient sealing technologies, Caterpillar hydraulic pumps achieve high levels of energy efficiency. This not only reduces operating costs but also contributes to a more sustainable and environmentally friendly hydraulic system.
To ensure optimal performance, Caterpillar hydraulic pumps undergo rigorous testing and quality control processes. These tests evaluate factors such as flow rate, pressure capabilities, and overall efficiency. By meeting strict performance standards, Caterpillar pumps provide reliable and efficient operation in a wide range of applications.
By considering both performance and efficiency in their design, Caterpillar hydraulic pumps offer users the benefits of improved productivity, reduced energy consumption, and extended system life. Whether used in construction, mining, agriculture, or other industries, Caterpillar hydraulic pumps deliver reliable and efficient performance for demanding hydraulic systems.
Operating Principles of Caterpillar Hydraulic Pumps
Caterpillar hydraulic pumps operate based on fundamental principles that allow them to convert mechanical power into hydraulic power. Understanding these operating principles is crucial for utilizing these pumps effectively.
At the core of a Caterpillar hydraulic pump is a rotating element, such as a piston, vane, or gear, that is driven by an external power source, such as an engine or an electric motor. As this rotating element spins, it creates a suction effect that draws hydraulic fluid from the reservoir into the pump’s inlet.
Once the fluid enters the pump, it is trapped between the rotating element and the pump housing. As the rotating element continues to spin, it moves the fluid along, gradually increasing its pressure. This is achieved through a combination of displacement and positive displacement principles, depending on the type of pump.
As the fluid is pressurized, it is forced out of the pump through the outlet port, ready to be utilized in the hydraulic system. The flow rate and pressure of the fluid can be controlled through various mechanisms, such as valves and regulators, allowing for precise control of the hydraulic system’s operation.
Components like pistons, cylinders, and valves play critical roles in the pump’s operation. Pistons create the displacement needed to pressurize the fluid, while valves regulate the flow and direction of the fluid within the pump. These components work together in a coordinated manner to ensure efficient and reliable hydraulic power generation.
By understanding the operating principles of Caterpillar hydraulic pumps, operators and technicians can effectively control and harness the power of these pumps in their hydraulic systems. This knowledge enables them to optimize system performance, respond to varying load conditions, and ensure the safe and efficient operation of the equipment.
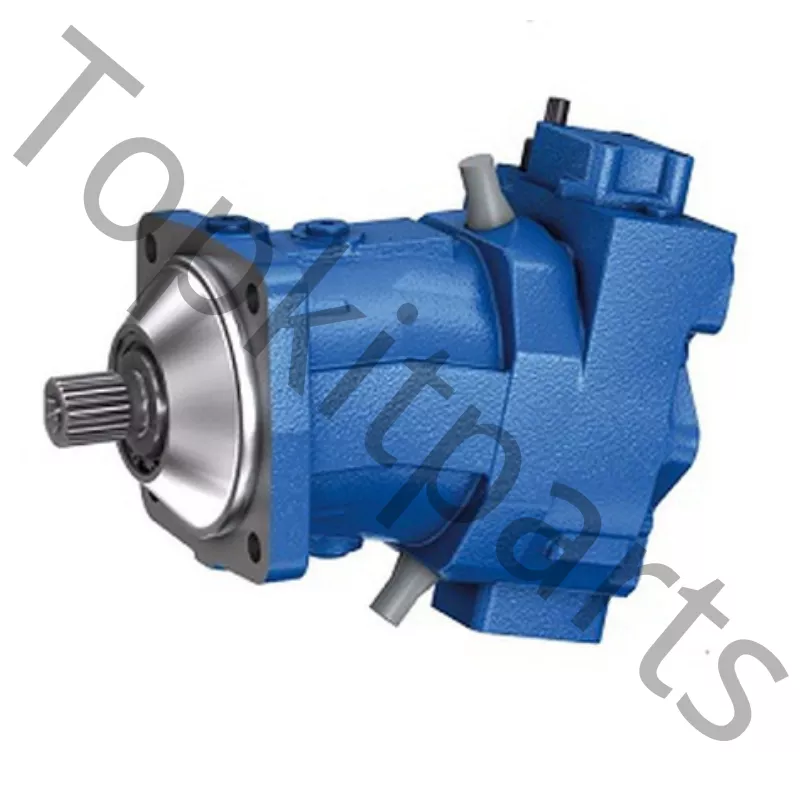
Control and Regulation of Hydraulic Power
Caterpillar hydraulic pumps are equipped with advanced control and regulation mechanisms to maintain optimal performance and ensure efficient operation of hydraulic systems. These systems play a crucial role in controlling the flow, pressure, and direction of hydraulic power.
One of the key components in hydraulic power control is the valve system. Caterpillar hydraulic pumps employ various types of valves, such as pressure relief valves, directional control valves, and flow control valves. These valves allow for precise adjustment of the hydraulic power output, ensuring that it meets the specific requirements of the system.
In addition to valves, Caterpillar hydraulic pumps utilize sensors and control systems to monitor and regulate hydraulic power. Sensors provide feedback on parameters such as pressure, temperature, and flow rate, allowing the control system to make real-time adjustments as needed. This ensures that the hydraulic system operates within safe limits and delivers consistent performance.
The control system in Caterpillar hydraulic pumps may include electronic controls and programmable logic controllers (PLCs). These sophisticated systems enable precise control over hydraulic power delivery, allowing for automation and integration with other equipment or systems.
Precise control and regulation of hydraulic power offer several benefits. It ensures that the hydraulic system operates efficiently, minimizing energy losses and optimizing overall system performance. It also allows for smooth and accurate control of actuators, enabling precise movement and positioning in various applications.
Proper maintenance and calibration of the control and regulation components are essential for reliable and accurate hydraulic power control. Regular inspections, sensor calibration, and software updates are necessary to ensure the continued functionality and effectiveness of these systems.
By incorporating advanced control and regulation mechanisms, Caterpillar hydraulic pumps provide operators with the tools to optimize hydraulic power delivery, enhance equipment performance, and achieve precise control in a wide range of applications.
In conclusion, understanding the engineering principles behind Caterpillar hydraulic pumps is essential for maximizing their performance and efficiency in hydraulic systems. The design, construction, and operation of these pumps rely on a combination of fundamental hydraulic principles and advanced engineering techniques.
Throughout this outline, we have explored the fundamentals of hydraulic systems, the design and construction considerations of Caterpillar hydraulic pumps, and the factors that influence their performance and efficiency. We have also discussed the operating principles of these pumps and the control and regulation mechanisms employed to ensure optimal power delivery.
By comprehending the engineering principles behind Caterpillar hydraulic pumps, operators and maintenance personnel can make informed decisions regarding their use, maintenance, and troubleshooting. This knowledge enables them to achieve optimal performance, minimize downtime, and extend the lifespan of the hydraulic pumps.
As hydraulic systems continue to play a vital role in various industries, it is crucial to stay updated with the latest advancements in hydraulic pump technology. By fostering a deeper understanding of hydraulic system design and operation, we can unlock the full potential of Caterpillar hydraulic pumps and harness their capabilities for efficient and reliable power transmission.
We encourage further exploration and learning in this field, as it leads to continuous improvement and innovation in hydraulic system design, operation, and maintenance. By staying informed and leveraging the engineering principles behind Caterpillar hydraulic pumps, we can drive productivity, enhance equipment performance, and achieve optimal hydraulic system operation.
Related Keywords
#caterpillar hydraulic cylinder,#hydraulic pump for excavator,
#caterpillar excavator hydraulic system,
#cat hydraulic oil,
#rebuilt hydraulic pumps,
#who buys hydraulic pumps,